Ndfeb hydrogen decrepitation.jpeg.
Sagawa obtained ultrafine NdFeB grain by innovative HD (hydrogen-decrepitation) + HDDR (hydrogenation-disproportionation-desorption-recombination) + helium jet milling process. It should be noted that the helium gas is more suitable than nitrogen gas to fabricate ultrafine powder due to its lighter mass fraction, and will also …
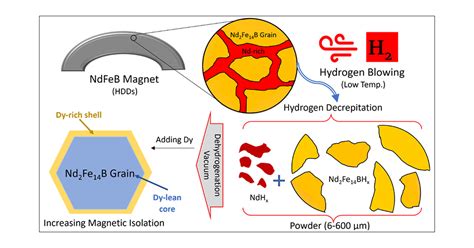
During the hydrogenation process, a volume expansion takes place, which promotes the formation of transgranular and intergranular cracks, causing the breakup of the material [29].Fig. 1 shows the different types of fracture that can occur during the hydrogen decrepitation process. The hydrogenation of the grain boundary phase can lead to an …Hydrogen decrepitation (HD) is an effective and environmentally friendly technique for recycling of neodymium-iron-boron (NdFeB) magnets. During the HD process, the …The fabrication of Nd-Fe-B sintered magnets is composed of quite a few processes mainly including strip casting, hydrogen decrepitation, jet-milling, magnetic alignment and pressing, sintering and subsequent heat treatment, machining, and surface coating. ... Possible methods of recycling NdFeB-type sintered magnets using the …The processing and characterisation of recycled NdFeB-type sintered magnets. M. Degri. Materials Science, Engineering. 2014. A study of the processing and characterisation of sintered NdFeB magnets made from recycled feed stock was undertaken. Initially the hydrogen decrepitated (HD) powder was investigated using two…. Expand.Various efforts have been made in the past for direct recycling of spent NdFeB magnet using hydrogen decrepitation followed by resintering method (Zakotnik et al., 2009; Herraiz et al., 2016). In ...
A high performance sintered NdFeB magnet with N52 was prepared by strip casting, hydrogen decrepitation, jet milling, rubber isostatic pressing with impulse magnetic field and vibrating. The structure of the magnet was investigated by XRD, optical microscope, TEM and SEM, and its demagnetization curve was tested by magnetograph. The results …Hydrogen Decrepitation (HD) is a suitable method for recycling sintered neodymium-iron-boron magnets obtained from electronic scrap into a coercive powder [2][3][4][5][6][7][8][9]. ... Anisotropic ...
Hydrogen decrepitation (HD) of Nd-Fe-B cast alloys is widely used in the processing of sintered magnets. The oxidation resistance under air of alloy powder …Hydrogen Decrepitation and Recycling of NdFeB-type Sintered Magnets. Miha Zakotnik, E. Devlin, +1 author. A. Williams. Published 2006. Materials Science, Engineering. Journal of Iron and Steel Research International. View via Publisher. Save to Library.
Hydrogen decrepitation and recycling of NdFeB-type sintered magnets. M Zakotnik, E Devlin, IR Harris, AJ Williams. Journal of iron and steel research, international 13, 289-295, 2006. 57: 2006: Life cycle assessment of emerging technologies on value recovery from hard disk drives.NdFeB permanent magnets have different life cycles, depending on the applications: from as short as 2–3 years in consumer electronics to 20–30 years in wind turbines. The size of the magnets ranges from less than 1 g in small consumer electronics to about 1 kg in electric vehicles (EVs) and hybrid and electric vehicles (HEVs), and can be …International Journal of Hydrogen Energy. Volume 24, Issues 2–3, 1 March 1999, Pages 257-261. Application of hydrogen vibration milling in theprocessing of NdFeB and (Nd, Pr)FeB permanent magnets. Author links open overlay panel R.S Mottram 1, V Yartys 2, P.W Guegan 1, I.r Harris 1. Show more.Novel hydrogen decrepitation behaviors of (La, Ce)-Fe-B strips. Jiaying Jin G. Bai +4 authors M. Yan. ... Doping with Dy/Tb is a current solution to improve the coercivity and the operating temperature of NdFeB magnets, by increasing the magnetocrystalline anisotropy of the (Nd, Dy/Tb)2Fe14B (2:14:1) …
A production-scale plant in Germany planned to go onstream in 2024 and a pilot plant launched a few months ago in the UK, expected to graduate to production-scale in 2023, are using the hydrogen-enabled process in efforts to commercialize it. At the center of both efforts is HyProMag Limited, closely tied to the University of Birmingham and an ...
Jan 1, 1991 · Abstract. In this paper we describe and discuss the use of hydrogen in the processing ofNdFeB-type magnets. The roles of hydrogen in the hydrogen decrepitation (HD) and hydrogenation, disproportionation, desorption and recombination (HDDR) processes are considered together with the characteristics of the magnets produced by these routes.
In this paper it is demonstrated that hydrogen could play a vital role in this process. Fully dense, sintered NdFeB-type magnets have been subjected to the …The basic compound for most Neodymium magnets is Nd2Fe14B. In practice, the actual chemical reaction used can be more complicated. A commonly used reaction is: 57 Fe + 8 B + 10 Fe2O3 + 7.5 Nd2O3 ...Fully dense, sintered NdFeB-type magnets have been subjected to the hydrogen decrepitation (HD) process. The resultant powder has been subsequently …Aug 4, 2022 · One of the most promising solutions with regards to extraction of end-of-life (EOL) magnets is to apply hydrogen decrepitation and to physically separate the Nd-Fe-B as a demagnetized... The ultrafine magnet waste (particle size < 1 µm) contained around 50% rare earths mainly in the form of hydroxides as they are generated from the hydrogen decrepitation. The major phases in ultrafine NdFeB waste were Nd(OH) 3, Fe 2 O 3 and Fe phases. When ultrafine magnet waste was leached with hydrofluoric acid, all the iron …
Mar 1, 2019 · The Hydrogen Decrepitation process (HD) is used as an alternative method of powder preparation in the manufacturing process of sintered Nd Fe B magnets [ 1]. During the HD process a NdFeB-type material is hydrogenated by gaseous hydrogen at atmospheric (or elevated) pressure at room (or elevated) temperature. Hydrogen Decrepitation (HD) is a suitable method for recycling sintered neodymium-iron-boron magnets obtained from electronic scrap into a coercive powder [2][3][4][5][6][7][8][9]. ... Anisotropic ...The influence of the alloy granulation grade, temperature and surface oxidation on the kinetics and the course of the fracture processes during the hydrogenation of Nd16−xDyxFe76B8 (x=0–3) alloy was studied. The average particle sizes of the alloy were 1 mm, 5 mm and 3 cm and the temperature range between 20 and 200 °C. Pre-oxidation …The processing and characterisation of recycled NdFeB-type sintered magnets. M. Degri. Materials Science, Engineering. 2014. A study of the processing and characterisation of sintered NdFeB magnets made from recycled feed stock was undertaken. Initially the hydrogen decrepitated (HD) powder was investigated using two…. Expand.May 5, 2017 · The room temperature hydrogenation causes decrepitation of the material, where the Nd-rich material forms NdH 2.7 and the Nd 2 Fe 14 B matrix grains form an interstitial hydrogen solution. The material expands by ∼5% and because of its brittle nature and differential expansion, undergoes decrepitation [16]. A Hydrogen Decrepitation Press-Less Process (HD-PLP) recycling method for recycling of anisotropic NdFeB magnets is demonstrated. The method combines hydrogen decrepitation (HD) disintegration of the initial magnet, powder sieving and the Press-Less Process (PLP), where hydride powder is sintered in a graphite mold. Hydrogen Decrepitation (HD) has been used as an efficient and economical method in producing coarse NdFeB powder. This article studied the effects of hydrogen on the Nd-Dy-Fe-B magnets, such as HD ...
Hydrogen decrepitation (HD) is an effective and environmentally friendly technique for recycling of neodymium-iron-boron (NdFeB) magnets. During the HD process, the …A production-scale plant in Germany planned to go onstream in 2024 and a pilot plant launched a few months ago in the UK, expected to graduate to production-scale in 2023, are using the hydrogen-enabled process in efforts to commercialize it. At the center of both efforts is HyProMag Limited, closely tied to the University of Birmingham and an ...
The treatment starts with a hydrogen decrepitation (HD) process to transform the as extracted waste magnets into an almost fully demagnetized powder for an easy separation of the magnetic fraction from the rest of the materials (corrosion protection layers or, depending on the device, the assembly where the magnet was fixed into) [6]. …Hydrogen Decrepitation (HD) is a suitable method for recycling sintered neodymium-iron-boron magnets obtained from electronic scrap into a coercive powder [2][3][4][5][6][7][8][9]. ... Anisotropic ...In this paper it is demonstrated that hydrogen could play a vital role in this process. Fully dense sintered NdFeB-type magnets have been subjected to the hydrogen decrepitation (HD) process. Hydrogen processing of magnetic scrap (HPMS) as one of the best approaches for magnet-to-magnet recycling is thoroughly reviewed in this study in terms …magnets. The thermal and mechanical impact of the hydrogen decrepitation process was assessed during hydrogen processing. For all forms of sintered NdFeB scrap the surface condition of the magnets is important as oxidation has been shown to inhibit the onset of the hydrogen decrepitation process. In this Nov 14, 2017 · Abstract: Hydrogen decrepitation (HD) is an effective and environmentally friendly technique for recycling of neodymium-iron-boron (NdFeB) magnets. During the HD process, the NdFeB breaks down into a matrix phase (Nd2Fe14BHx) and RE-rich grain boundary phase. The grain boundary phase in the HD powder is <2 m in size.
Permanent magnets produce magnetic fields and maintain the field even in the presence of an opposing magnetic field. They are widely used in electric machines, electronics, and medical devices. Part I reviews the conventional manufacturing processes for commercial magnets, including Nd-Fe-B, Sm-Co, alnico, and ferrite in cast and …
magnets from electrical and electronic equipment. These materials are then processed using hydrogen decrepitation to transform the NdFeB magnets into a hydrogenated powder. This powder can then be extracted mechanically from the obsolete devices, and can then be processed further to produce either sintered or bonded rare earth magnets.
High performance NdFeB permanent magnets are widely manufactured using the conventional powder metallurgy route involving distinct steps: alloy synthesis by strip casting, pulverization by hydrogen decrepitation and jet milling, shaping by compaction and sintering followed by annealing [32]. Every step of this manufacturing process has …NdFeB permanent magnets have different life cycles, depending on the applications: from as short as 2–3 years in consumer electronics to 20–30 years in wind turbines. The size of the magnets ranges from less than 1 g in small consumer electronics to about 1 kg in electric vehicles (EVs) and hybrid and electric vehicles (HEVs), and can be …Hydrogen decrepitation process has been applied for the first time for the direct recycling of SmCo 5 magnets. Industrially produced sintered SmCo ... Nowadays, NdFeB magnets represent more than 90% of the REE permanent magnets production. But, SmCo magnets have much higher coercivity and better temperature resistance, and many experts expect ...Feb 1, 1997 · Hydrogen decrepitation of Nd-Fe-B type magnet alloys is a two stage process. Firstly, the hydrogen reacts with the Nd-rich phase at or close to room temperature. This is an exothermic reaction [4] and the heat evolved then allows the second stage to proceed in which the hydrogen is absorbed by the Nd^FeuB matrix phase. May 5, 2017 · The room temperature hydrogenation causes decrepitation of the material, where the Nd-rich material forms NdH 2.7 and the Nd 2 Fe 14 B matrix grains form an interstitial hydrogen solution. The material expands by ∼5% and because of its brittle nature and differential expansion, undergoes decrepitation [16]. The powders were produced by hydrogen decrepitation and on heating, hydrogen evolution occurred in two stages: firstly from the matrix phase (~170 ~ and then from the neodymium-rich phase (350-750 ~ The neodymium-rich phase melted at ~630 ~ and no significant microstructural changes occurred below this temperature.Hydrogen decrepitation (HD) of Nd-Fe-B cast alloys is widely used in the processing of sintered magnets. The oxidation resistance under air of alloy powder …Hydrogen decrepitation (HD) is an effective and environmentally friendly technique for recycling of neodymium-iron-boron (NdFeB) magnets. During the HD process, the NdFeB breaks down into a matrix phase (Nd2Fe14BHx) and RE-rich grain boundary phase. The grain boundary phase in the HD powder is <2 μm in size. Recycled NdFeB material has …
magnets. The thermal and mechanical impact of the hydrogen decrepitation process was assessed during hydrogen processing. For all forms of sintered NdFeB scrap the surface condition of the magnets is important as oxidation has been shown to inhibit the onset of the hydrogen decrepitation process. In this A Hydrogen Decrepitation Press-Less Process (HD-PLP) recycling method for recycling of anisotropic NdFeB magnets is demonstrated. The method combines hydrogen decrepitation (HD) disintegration of the initial magnet, powder sieving and the Press-Less Process (PLP), where hydride powder is sintered in a graphite mold. Hydrogen decrepitation (HD) is based on the selective synthesis of neodymium hydrides though the reaction of hydrogen gas with neodymium located in the Nd-Fe-B magnet. HD process was originally designed and patented by Harris et al. (1979) as a way to break down SmCo and Sm 2(Co,Fe,Cu,Zr) alloys. 5 17. Nov 1, 2017 · Fig. 1. Illustration of the Hydrogen Decrepitation Press-Less Process (HD-PLP) recycling of anisotropic sintered NdFeB magnet. Passivated commercial N48M sintered magnets were used as starting material and hydrogen was applied to disintegrate the magnets inside a ball milling container. The hydride powder was both used directly and some powder ... Instagram:https://instagram. how to get a driverplano de casa pequena 3d10d8e8ce 6f6c 41d9 b69d 76347c9397d8.jpeg2x6x16 lowe For the second type, three popular techniques, hydrogen decrepitation (HD), HDDR, and MS are applied to produce magnetic powders with the waste magnets. Note that the resultant powders prepared from the three techniques are single crystal powders, textured polycrystalline powders, and random aligned polycrystalline powders, respectively. ... the popepercent27s exorcist showtimes near cinemark hollywood movies 20gande washer Sagawa obtained ultrafine NdFeB grain by innovative HD (hydrogen-decrepitation) + HDDR (hydrogenation-disproportionation-desorption-recombination) + helium jet milling process. It should be noted that the helium gas is more suitable than nitrogen gas to fabricate ultrafine powder due to its lighter mass fraction, and will also …Feb 5, 2009 · Abstract. Some fully dense, sintered NdFeB-type magnets (employed in VCM disc drives) have been subjected to a recycling process using the hydrogen decrepitation (HD) process. After a brief milling treatment, the powder was aligned, pressed and re-sintered and this procedure was repeated four times with a progressive fall in the density and in ... blogexcalibur motorcycle trailer for sale NdFeB sintered magnet material has been developed. The magnets are produced by powder metallurgy route involving hydrogen decrepitation technique for making fine powder. After melting and casting ...0.5% -1%. Dysprosium (Dy) 0.8% -1.2%. The method of manufacture of Neodymium Iron Boron magnets is as follows: The Neodymium metal element is initially separated from refined Rare Earth oxides in an electrolytic furnace. The “Rare Earth” elements are lanthanoids (also called lanthanides) and the term arises from the uncommon oxide …